Top 15 Digital Technologies in Manufacturing Industry
Based on the analysis of big data, the Institute for Statistical Studies and Economics of Knowledge (ISSEK) of the Higher School of Economics has identified the most significant digital technologies already used or introduced in the global and Russian manufacturing industry.
In the modern manufacturing industry, digital technologies are used at all stages of the life cycle, from concept idea, design, production, and operation to service and disposal. Reliance on digitalization provides enterprises with significant competitive advantages, especially in an environment of uncertainty. Digitalization has played a critical role in 2020, when the most robotized, automated and telecommuting enterprises have been most effective in tackling the challenges of the COVID-19 pandemic.
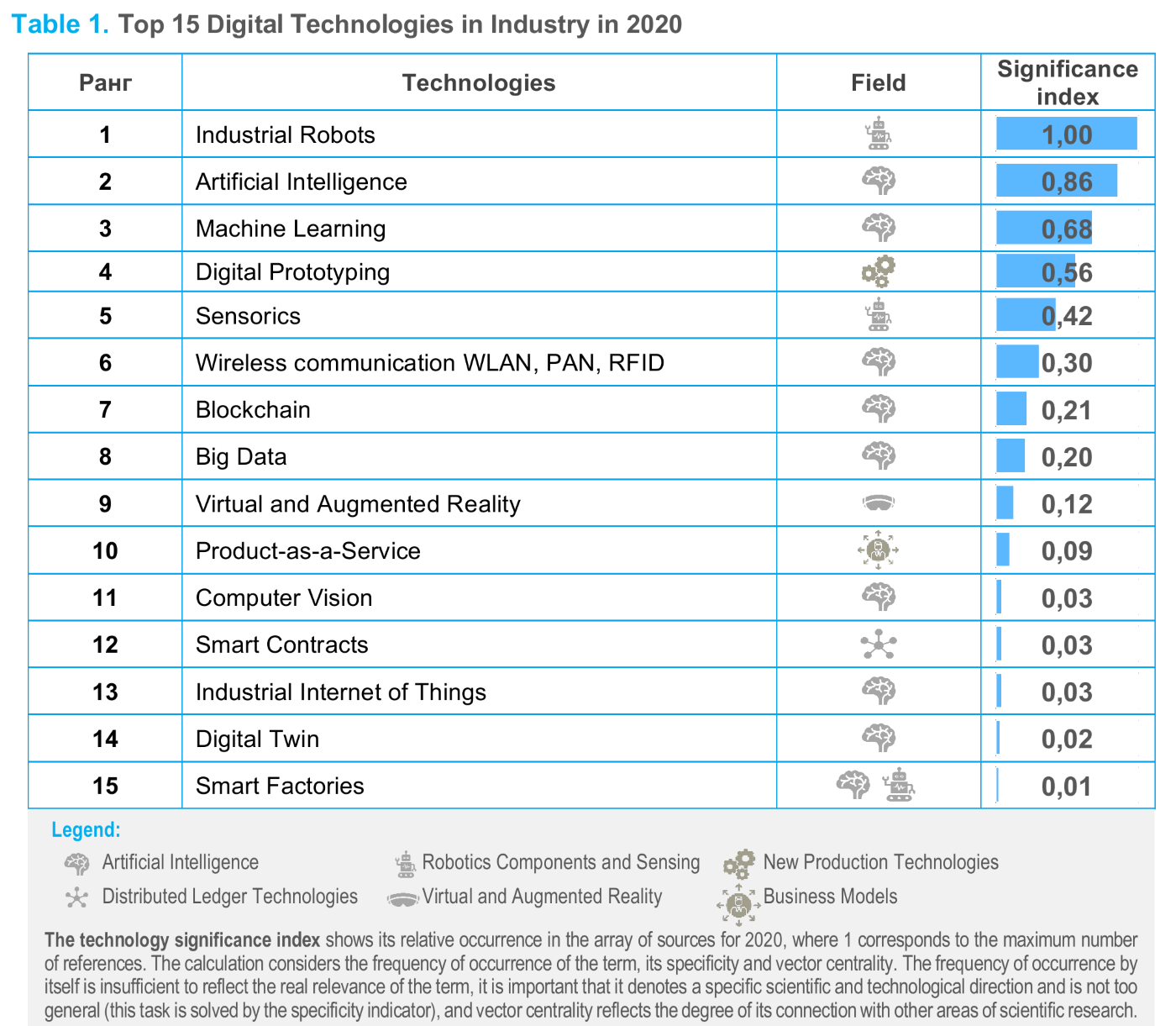
For reference: Calculations were made on the basis of more than 180 thousand authoritative foreign sources (publications in scientific journals presented on the Microsoft Academic Graph platform and industry media) using the iFORA big data mining system, developed by the HSE ISSEK using advanced artificial intelligence technologies. The iFORA information base includes more than 500 million documents (scientific publications, patents, regulatory framework, market analytics, industry media, materials of international organizations, vacancies and other types of sources) and is constantly updated. In 2020, iFORA is featured in Nature as an effective decision support tool for the benefit of business and government. The OECD ranks the system as a successful science digitalisation initiative.
Trends and Effects of the Application of Digital Technologies in Industry
Industrial robots (No. 1) that open the top 15 help to reduce labour costs, maintain a stable level of product quality, and increase the technological flexibility of production. In the Russian industry, robots are mostly used in the automotive industry, in chemical and petrochemical plants.
In the field of artificial intelligence (AI) (No. 2), a formidable leap has been made in recent years from the use of semi-autonomous robotic manipulators on flexible production lines to the control of autonomous vehicles moving in and between workshops. In the future, more and more advanced AI technologies will fully automate production processes and optimize the work of not only individual enterprises, but entire industries.
Machine learning (No. 3) technologies are increasingly being used in situations when it is either dangerous, or impossible, or ineffective to use human resources (for example, to work in hard-to-reach places, in conditions of permafrost or increased radiation, in hazardous chemical industries). They are also relied on when, as data sets on the condition of industrial equipment accumulate, it becomes impossible for people to predict its residual resource and critical malfunctions, to prevent sudden failures and to perform maintenance on condition.
For adaptive control of robot operations, solutions based on computer (machine) vision (No. 11) are used. For example, a Philips razor factory in the Netherlands looks like an unlit room with 128 robots monitored by only nine employees. Computer vision also helps to monitor the actions of personnel in terms of meeting safety requirements. Technologies for automatic fixation and processing of moving and stationary objects using computer tools are already able to determine in real-time, by video or photographic images, where a person and his body parts (head, hands, legs) are located, and to assess the correctness of wearing special clothing (gloves and helmets ), and in the near future, they will bring the work of enterprises to a qualitatively new level.
The introduction of the industrial Internet of things (No.13) dramatically increases the efficiency of production and significantly reduces the payback period of projects. Arrays of Big data (No. 8), obtained, in particular, from wireless IP-enabled devices, including smartphones, tablets, sensors, and other devices, are used in a wide range of applications. The main ones among them are forecasting the market situation, improving products, as well as optimizing marketing and sales. Blockchain-based supply chain tracking (No.7), smart contracts (No.12) and other electronic transactions, as well as marketplaces, are helping to strengthen industrial cooperation. By studying user experience based on data from wearable devices, enterprises are moving from ‘scheduled repair’ to ‘repair as needed’ in after-sales service, and in general are developing a Product-as-a-Service business model (No.10).
Designers, manufacturers and engineers use digital prototyping (No.4) to design products and visualize their entire manufacturing process. VR testing (No.9) allows you to reduce the time and cost of developing new products, test and improve product quality. Thus, thanks to the introduction of digital aircraft testing at virtual test ranges, PJSC UAC managed to almost halve the number of flights for debugging onboard systems.
Enterprises often combine the development of different technological directions. For example, to accelerate the creation and launch of products and services on the market, systems based on digital twins (No.14) of production processes are used, including elements of AI, the Internet of things, sensorics (No.5), as well as wireless telecommunication technologies (No.6). During operation, such systems help to optimize the operation of enterprises, minimize disruptions and shutdowns; according to the OECD estimates, they can predict the response of equipment to loads with an accuracy of 95% and reduce maintenance costs of complex industrial complexes by 5-10%. The annual growth of the digital twin market from 2020 to 2026, according to MarketsandMarkets, will be about 60%. Another vivid example of combining digital technologies is smart factories (No.15), fully automated (robotic) production, in which the management of all processes in real-time and taking into account constantly changing conditions is ensured by a combination of Internet of Things technologies, Big Data analysis and information management systems for production and business processes.
Sources: Calculations based on the iFORA big data mining system (copyright holder — HSE ISSEK); materials of the report ‘Digital transformation of industries: starting conditions and priorities’ (NRU HSE, 2021), released for the XXII April international scientific conference on the development of the economy and society; the results of the project ‘Application of semantic analysis of big text data to study development trends and dynamics of the spread of digital technologies’ of the thematic plan of research works, provided for by the State Assignment of the Higher School of Economics.
This study was conducted by N. N. Tarasova, P. O. Shparova
Translation by ICT. Moscow